Social
Quality Management
Quality Management
Quality Control
Best Quality Control
-
Producing high-quality products through quality management
- Obtained GMP certifications
- Established & monitoring the equipment optimized for GMP standards
- Conducting quality impact assessments
-
Established Quality Management System
- Established a quality control process
- Quality assurance system operation
-
Enhancing Quality Assurance
- Conducting quality assurance activities
- Providing training to enhance quality assurance capabilities
Enhancing Quality Control
Based on our quality-first management policy, SK bioscience is committed to strengthening the quality of our products throughout the entire value chain, from R&D and clinical trials to production, with a sense of responsibility that our products directly affect the lives of our customers. To this end, we operate a quality control process that controls and guarantees the entire pharmaceutical manufacturing process from raw material warehousing to final product shipment. In addition, we provide products that customers can trust by establishing and operating a quality management system. Moreover, we have secured excellent quality levels that are recognized at home and abroad by acquiring a certification from the United Kingdom of Great Britain’s Medicines and Healthcare products Regulatory Agency(MHRA), the European Medicines Agency(EMA)’s EU-GMP, as well as the Korean Good Manufacturing Practice(K-GMP).
Quality Control Process
-
Raw Material Warehousing
- Documentation of products/processes
- Establishment of quality policies
-
Drug Manufacturing
- Monitoring for production and process
- Based on the quality assurance system
-
Shipment Quality Assurance
- Product testing & quality assessment
- Performing qualification and validation
-
Customer Service Quality
- Analysis & response to defective drugs
- Establishing customer response strategies
Quality Management System
Quality Assurance System Operation
Providing customers with reliable products and services of the highest quality is an essential requirement for the sustainable growth of a company. SK bioscience operates a strict quality management system that covers all stages of the product life cycle, from product development to consumer use. Our quality assurance system is optimized to continuously produce, manage, and sell pharmaceutical products in a Good Manufacturing Practice(GMP) environment. In addition, we manage issues such as deviations and complaints with a system to produce high-quality pharmaceuticals. We also perform qualification and validation of all facilities and equipment to ensure their performance and functionality. As such, we have established a quality policy to comply with all customer and legal requirements, as well as standards for quality assurance, facilities/equipment, raw materials, manufacturing control, packaging/labeling, and test management. Moreover, we raise the awareness of quality personnel by specifying essential compliance requirements in documents.
Quality System
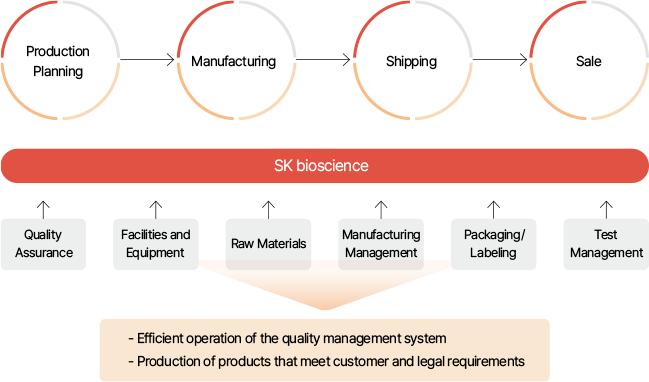
Quality Management Promotion System
SK bioscience has a system in place to ensure the smooth operation of the quality assurance system and GMP. Based on its annual and factory quality training systems, the Quality Assurance(QA) division supports risk analysis for quality management, performs deviation handling procedures, and operates a preventive action system. It also conducts evaluation and monitoring for installation, calibration, and maintenance of GMP-compliant facilities and equipment. Moreover, it oversees general quality management tasks such as product recall notification/investigation/record storage, supplier audit, and purchase change approval. The Quality Control(QC) division examines raw materials, intermediate process samples, and final drug substances used in pharmaceutical manufacturing to check whether the specifications have been met. In this process, physics and chemistry, microbiology, animal testing, and device analysis tests are conducted according to Standard Operating Procedure(SOPs). To this end, it carries out test method validation and management activities to maintain the functions of the QC laboratory, such as device qualification and Computer System Validation(CSV). We are committed to continuous improvement of our quality system by monitoring our drug safety evaluation programs and manufacturing support facilities, regularly reporting the results to top management, and receiving feedback from management.
SK bioscience Quality Policy
- 1The quality organization must operate independently of the production organization.
- 2All employees who perform GMP must have appropriate qualifications and improve and maintain GMP level through training.
- 3All important manufacturing processes must be validated, and the quality standards established through validation must be reviewed regularly and kept up to date.
- 4All the facilities and systems required for GMP must be equipped.
- 5All work during the manufacturing process must be performed according to the approved method. All progress must be recorded and preserved in the manufacturing instructions and records.
- 6A recall system must be established and maintained
- 7A complaint handling system must be kept in place, the cause of complaints that arise should be investigated. Appropriate measures to prevent the recurrence of the same complaints must be taken.
Enhancing Quality Assurance
Quality Assurance Activities
SK bioscience pays special attention to diagnosing and managing product quality risks as we produce vaccine raw materials and finished drugs that are sensitive to temperature and environment. Products are stored and monitored at specified temperatures and environments. Commercialized products undergo annual safety tests to check their quality. Raw materials are also managed under proper storage conditions. In addition, for GMP compliance and process control, critical processes are managed and supervised onsite based on product standards, manufacturing records, and a guidebook. Moreover, QA on the shop floor policy* is implemented to ensure data integrity, and process deviations are handled on-site in real-time. We continuously manage whether quality issues are improved and whether operations are in line with global GMP standards by conducting a quality impact assessment of products in the first half of each year. A validated eQMS is applied to the quality assurance system, allowing for comprehensive management of changes, deviations, corrections, and prevention, as well as deviations from standards, to be tracked in real time.
- * The QA on the Shop Floor Policy: A system that enables quality assurance personnel to participate directly in key processes to solve or respond promptly to problems when they occur. It is operated to prevent unnecessary process deviations.
Enhancing Quality Assurance Capabilities
We conduct quality assurance capacity-building training for product quality managers. We conduct regular training to strengthen GMP competencies. And new employees receive basic training and on-the-job training to ensure they have the necessary skills for their respective jobs. Jobs that require special capabilities, such as quality testing and aseptic work, are strictly managed to ensure that only authorized employees perform such tasks through verification and qualification procedures. Therefore, our training programs provide not only training on common competencies such as quality system operation, production procedures, hygiene, and dress code but also detailed training for each specific job, as well as training to enhance the capabilities of each employee.